Bearing Installation and Maintenance

Introduction
Bearings play a vital role in ensuring the smooth operation of machinery across various industries, from manufacturing and automotive to aerospace and heavy equipment. Their efficiency and durability depend not only on their quality but also on proper installation and regular maintenance. Incorrect handling, misalignment, inadequate lubrication, or contamination can lead to premature failure, increased downtime, and costly repairs.
To maximize performance and extend the lifespan of bearings, it is essential to follow best practices in installation, maintenance, and troubleshooting. This guide provides key insights into proper bearing handling, lubrication methods, common installation mistakes to avoid, and effective maintenance strategies, helping industries achieve optimal efficiency and reliability.
Proper installation and maintenance extend the life and efficiency of bearings. Key considerations include:
- Installation Techniques – Press fit, thermal expansion, and hydraulic mounting methods.
- Maintenance Practices – Lubrication, periodic inspection, and cleaning processes.
- Common Bearing Failures – Causes include misalignment, overloading, poor lubrication, and contamination
1. Bearing Installations

Proper installation is crucial to ensure the longevity, efficiency, and reliability of bearings. Incorrect installation can result in premature failure, increased friction, and reduced performance. Following the correct procedures helps optimize bearing lifespan and machine efficiency.
Key Steps in Bearing Installation
1. Inspection Before Installation
- Check for physical defects, rust, or contamination.
- Ensure correct bearing type and size for the application.
- Use clean, dry, and debris-free environments for installation.
- Wear clean gloves to prevent contamination.
- Avoid dropping or mishandling bearings to prevent internal damage.
- Use specialized tools instead of hammering the bearing in place.
- Press Fit Method
- Suitable for small bearings that require precise positioning.
-
- Uses a press tool to apply even pressure.
- Avoid excessive force to prevent damage.
- Thermal Expansion Method
-
- Heating the bearing slightly expands its diameter for easy mounting.
- Ideal for tight-fitting inner rings on shafts.
- Use controlled heating techniques (e.g., induction heaters) to avoid overheating.
- Hydraulic Method
-
- Uses oil pressure to smoothly mount large bearings.
- Reduces installation force and minimizes risk of bearing damage.
- Commonly used for industrial and heavy-duty applications.
Best Practices for Bearing Installation
✔ Follow Manufacturer Guidelines – Ensures correct fitting and optimal performance.
✔ Lubricate Correctly – Reduces friction and prevents overheating.
✔ Ensure Proper Alignment – Misalignment reduces lifespan and increases wear.
✔ Monitor Temperature & Pressure – Prevents thermal expansion damage.
Common Installation Mistakes & How to Avoid Them
❌ Dirty Installation Environment → ✅ Work in a clean, dust-free area.
❌ Overheating Bearings → ✅ Use controlled heating methods within safe limits.
❌ Misalignment → ✅ Ensure proper alignment during mounting.
Future Trends in Bearing Installation
- Automated Bearing Installation – Reduces human error and improves consistency.
- Smart Installation Tools – Use real-time data to optimize fit and alignment.
- AI & Sensor-Driven Monitoring – Helps predict and prevent installation issues.
2. Bearing Maintenance and Longevity
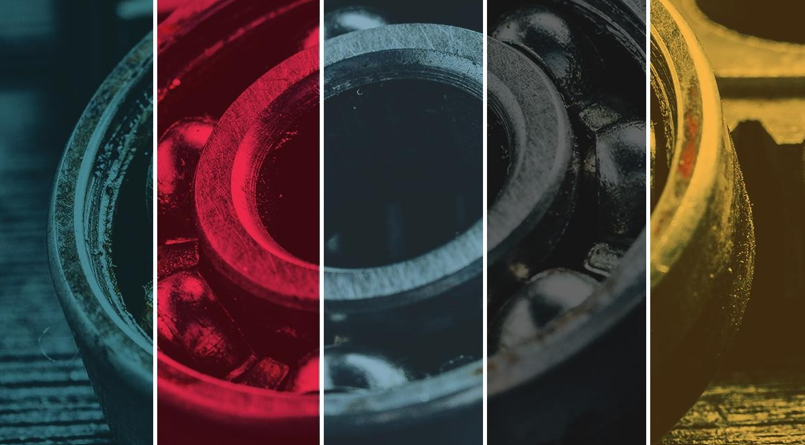
Regular bearing maintenance is essential to extend their lifespan, prevent unexpected failures, and ensure optimal machine performance. Proper maintenance reduces friction, wear, and contamination, which can lead to costly breakdowns.
Key Maintenance Practices for Bearings
1. Lubrication
-
-
- Types of lubrication:
- Grease Lubrication – Ideal for sealed and shielded bearings.
- Oil Lubrication – Used in high-speed or high-temperature applications.
- Best Practice: Apply the right lubricant at the recommended intervals to ensure smooth operation.
- Types of lubrication:
-
- Regular checks help detect early signs of wear, misalignment, or contamination.
- Key aspects to inspect:
- Misalignment – Causes uneven wear and increased stress.
- Vibration & Noise – Indicates potential bearing failure.
- Overheating – A sign of insufficient lubrication or excessive load.
-
-
- Prevents dust, debris, and dirt accumulation, which can cause damage.
- Best Practice:
- Use approved cleaning agents and avoid water-based cleaners that cause rust.
- Dry bearings thoroughly and apply lubricant before reinstalling.
-
-
-
- Protects bearings from dust, moisture, and contaminants that cause premature wear.
- Common Protection Methods:
- Sealed Bearings – Have built-in protection against contamination.
- External Seals & Shields – Used for open bearings in harsh environments.
-
Key Benefits of Regular Bearing Maintenance
✔ Prolongs Bearing Life – Reduces wear and minimizes failures.✔ Prevents Costly Downtime – Ensures machines run efficiently.
✔ Improves Performance – Enhances smooth operation and reliability.
✔ Reduces Energy Consumption – Proper lubrication lowers friction and heat.
Latest Innovations in Bearing Maintenance
- Automatic Lubrication Systems – Ensure consistent lubrication without manual effort.
- Predictive Maintenance with Sensors – Detects early wear using vibration and temperature monitoring.
- Advanced Coatings – Enhance durability and resistance to extreme conditions.
3. Causes of Bearing Failure
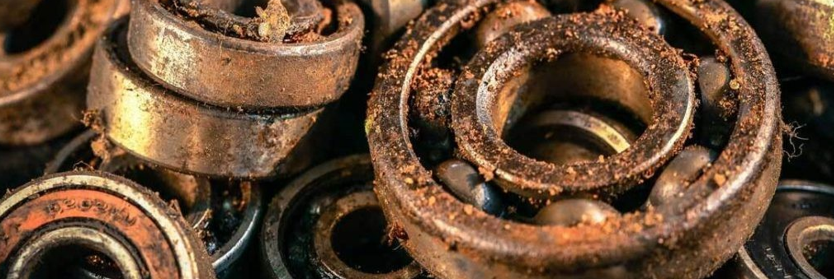
Bearings are essential components in machinery, but various factors can lead to their premature failure. Understanding these failure modes helps in preventing breakdowns, reducing maintenance costs, and improving equipment reliability.
Common Causes of Bearing Failure
1. Contamination
- Dirt, dust, and foreign particles penetrate the bearing, causing abrasion and premature wear.
- Common Sources:
- Improper handling and installation.
- Inadequate sealing against external elements.
- Prevention:
- Use sealed or shielded bearings in contaminated environments.
- Maintain clean workspaces during bearing installation.
- Using the wrong lubricant or insufficient lubrication results in excessive friction and overheating.
- Effects:
- Increased wear and risk of seizure.
-
-
-
- Higher energy consumption due to excessive friction.
- Prevention:
- Use the correct type and amount of lubrication as recommended.
- Monitor lubrication levels and apply at regular intervals.
-
-
- Excessive loads exceed the bearing’s capacity, leading to deformation and early fatigue failure.
- Common Causes:
- Incorrect bearing selection for the application.
- Sudden impact loads from heavy-duty operations.
- Prevention:
- Use bearings with appropriate load ratings.
- Reduce shock loads with proper damping systems.
- Occurs when the bearing, shaft, or housing is not properly aligned, leading to uneven load distribution.
- Effects:
- Increased friction and localized stress.
- Shortened bearing lifespan due to wear.
- Prevention:
- Ensure proper shaft and housing alignment during installation.
- Use self-aligning bearings for applications prone to misalignment.
-
-
- Moisture, chemicals, and humidity cause rust and pitting on bearing surfaces, leading to premature failure.
- Common Causes:
- Exposure to water, acids, and corrosive environments.
- Improper storage of bearings.
- Prevention:
- Use corrosion-resistant materials (stainless steel, coated bearings).
- Store bearings in dry, controlled environments.
-
✔ Unusual Noise – Grinding, clicking, or squealing sounds indicate wear.
✔ Increased Vibration – A sign of misalignment, imbalance, or contamination.
✔ Overheating – Excess friction due to poor lubrication or overload.
✔ Visible Wear or Rust – Pitting, scoring, or discoloration signals degradation.
Latest Innovations to Prevent Bearing Failure
- Smart Bearings with Sensors – Monitor temperature and vibration for early failure detection. Advanced Sealing Technology – Improved protection against contaminants and moisture.
- High-Performance Coatings – Enhance resistance to wear, corrosion, and extreme conditions.
Lubrication is essential for bearing performance, as it reduces friction, wear, and overheating. Proper greasing techniques extend bearing life and prevent premature failures.
Steps for Effective Bearing Greasing
1. Choose the Right Grease
-
-
- Select grease based on temperature, speed, and load requirements.
- Common types:
- Lithium-based grease – General-purpose and widely used.
- High-temperature grease – Suitable for industrial and automotive applications.
- Food-grade grease – Used in food processing machinery for safety compliance.
-
-
-
- Under-greasing – Leads to increased friction and wear.
- Over-greasing – Causes heat buildup, leakage, and contamination.
- Guideline:
-
-
-
-
- Follow manufacturer recommendations on the proper fill volume.
- In general, bearings should be filled to 30-50% of their internal space.
-
-
-
-
- Ensures consistent application across bearing surfaces.
- Steps to use a grease gun properly:
- Clean the grease fitting to prevent contamination.
- Slowly inject grease while rotating the bearing for even distribution.
- Monitor excess grease leakage as a sign of over-application.
-
-
-
- Bearings lose lubrication over time due to heat, load, and speed.
- Best practices for re-lubrication:
- Check the manufacturer’s recommended intervals.
- High-speed bearings require more frequent greasing.
- Avoid mixing different greases unless they are compatible.
-
Key Benefits of Proper Greasing
✔ Prevents Contamination – Protects against dust, moisture, and debris.
✔ Enhances Bearing Lifespan – Lowers the risk of premature failure.
✔ Improves Equipment Performance – Ensures smooth and efficient operation.
Latest Innovations in Bearing Lubrication
- Automatic Lubricators – Delivers precise lubrication at set intervals.
- Nano-Lubricants – Improves wear resistance and extends grease life
- Condition Monitoring Sensors – Detects grease degradation for predictive maintenance.
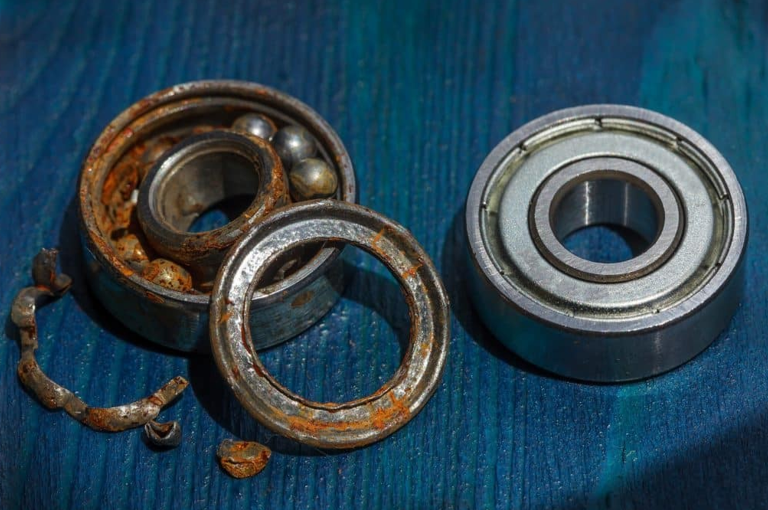
Bearings are critical components in machinery, but they can fail due to various factors. Understanding the common causes of bearing failure can prevent breakdowns, reduce downtime, and extend service life.
1. Poor Lubrication (Most Common Cause)
🔹 Effect: Increases friction, wear, and overheating.
🔹 Causes:
-
- Using the wrong type of lubricant.
- Insufficient lubrication or over-lubrication.
- Deterioration of grease or oil over time.
✔ Use manufacturer-recommended lubricants.
✔ Follow a regular re-lubrication schedule.
✔ Store lubricants properly to avoid contamination.
🔹 Effect: Causes premature wear and surface damage.
🔹 Causes:
-
- Exposure to dirty or wet environments.
- Improper handling and storage of bearings.
- Seals or shields damaged or missing.
✔ Use sealed or shielded bearings in harsh environments.
✔ Store bearings in clean, dry areas.
✔ Implement proper sealing techniques to block contaminants.
3. Improper Installation
🔹 Effect: Misalignment and uneven load distribution lead to early failure.
🔹 Causes:
-
- Using excessive force during installation.
- Incorrect mounting methods (e.g., hammering bearings into place).
- Shaft and housing misalignment.
✔ Use proper installation techniques (press-fit, thermal, or hydraulic methods).
✔ Align shafts and housings correctly before mounting.
✔ Inspect bearings before installation for damage or defects.
4. Fatigue (Repeated Stress on Bearing Materials)
🔹 Effect: Causes cracks, surface spalling, and eventual breakdown.
🔹 Causes:
-
- Bearings exceeding load capacity.
- Prolonged exposure to high speeds or extreme forces.
- Improper lubrication increases material stress.
✔ Choose bearings rated for the correct load and speed.
✔ Use high-quality materials designed for long-term durability.
5. Vibration & Shock Loads
🔹 Effect: Accelerates wear, leading to internal damage and reduced lifespan.
🔹 Causes:
-
- Operating machinery at high vibration levels.
- Sudden impact loads from heavy-duty applications.
- Imbalanced rotating components.
✔ Use vibration-dampening mounts to stabilize machinery.
✔ Perform regular balancing checks on rotating equipment.
✔ Choose heavy-duty bearings for applications with frequent shock loads.
Key Takeaways: How to Prevent Bearing Failure
- Proper Lubrication – Use the right grease/oil and maintain lubrication schedules.
- Contamination Control – Keep bearings clean and use seals or shields.
- Correct Installation – Avoid excessive force and ensure alignment.
- Monitor Fatigue – Replace bearings before failure using predictive maintenance.
- Reduce Vibration – Stabilize machinery and avoid sudden impact loads.
Advancements in Bearing Failure Prevention
🔍 AI & IoT Sensors – Real-time monitoring to detect issues before failure.🛠 Self-Lubricating Bearings – Reduces maintenance in industrial applications.📊 Vibration Analysis Technology – Predicts failures early for preventive maintenance.
By addressing these common issues, industries can improve machinery reliability, reduce downtime, and extend bearing lifespan.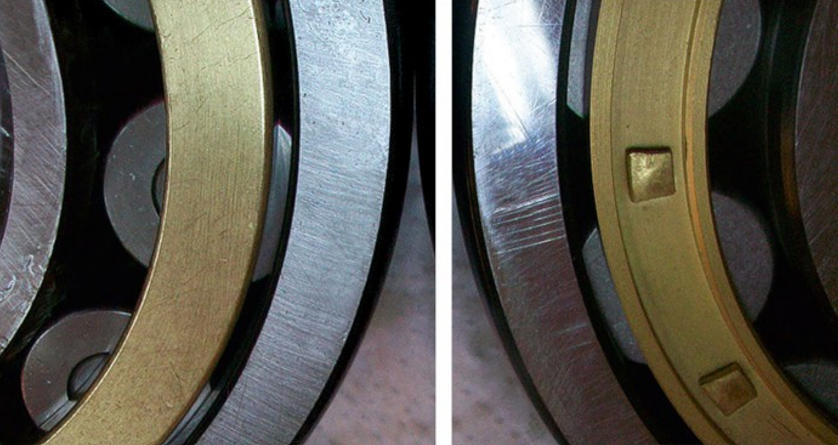
Counterfeit bearings can severely affect machine performance, leading to premature failure and safety risks. Identifying genuine bearings is crucial for reliability and durability.
Key Indicators of Authentic Bearings
1. Check the Packaging
-
-
- Genuine bearings come in high-quality, well-printed packaging with no blurry logos or misspelled words.
- Seals and holographic stickers are often present for brand authentication.
-
-
-
- Authentic bearings have clear, precise, and consistent branding, model numbers, and serial codes.
- Counterfeit bearings may have smudged, uneven, or missing engravings.
-
- Fake bearings may be lighter or have incorrect measurements due to low-quality materials.
- Use a caliper or micrometer to verify dimensions against official specifications.
- Always buy from certified suppliers or brand-authorized dealers to ensure authenticity.
- Be cautious of sellers offering unusually low prices.
- Genuine bearings meet ISO, ANSI, or JIS industry standards.
- Manufacturers provide certificates of authenticity and compliance upon request.
✔ Better performance – Ensures smooth operation and minimal friction.
✔ Safety assurance – Prevents machine failure and accidents.
✔ Manufacturer warranty – Guarantees quality and after-sales support.
Common Signs of Counterfeit Bearings
- Cheap-looking packaging – Thin cardboard, misprints, or poor-quality labels.
- Lack of documentation – Missing datasheets or warranty certificates.
- Inconsistent engraving – Uneven, faded, or misplaced brand markings.
- Unusual noise and roughness – Fake bearings wear out quickly and may feel grainy when rotated.
Conclusion: Bearing Installation and Maintenance
Mar 28,2025